The Advantages of Using a Pump System When Spraying Compared to a Gravity-Fed Pot Gun
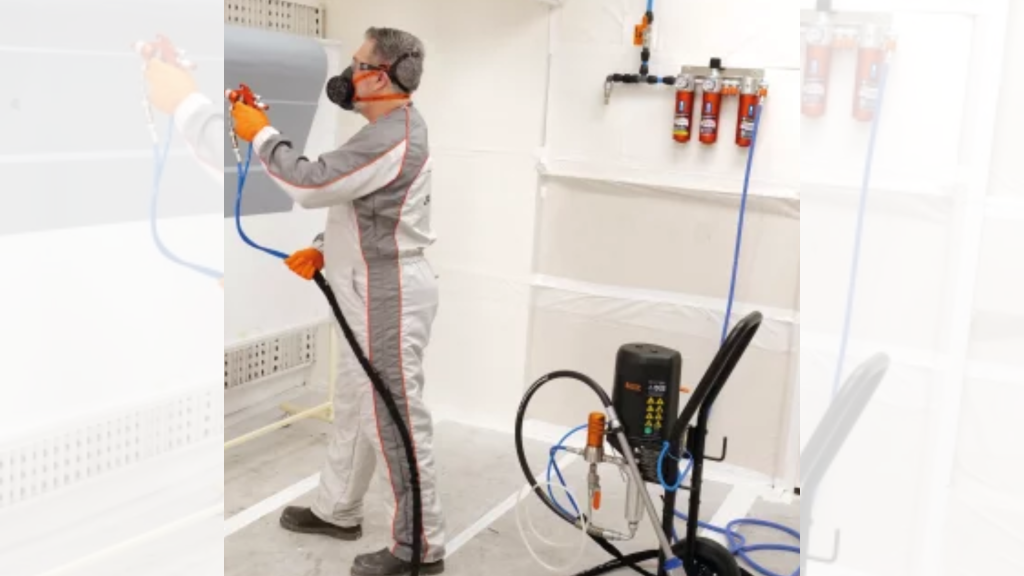
In the world of industrial and professional spray coating, choosing the right spray system can make a big difference in efficiency, finish quality, and overall productivity. While gravity-fed pot guns are commonly used due to their simplicity and affordability, pump systems offer several advantages that can greatly enhance spraying performance.
In this blog, we’ll explore the key benefits of using a pump system over a gravity-fed pot gun, and why it might be the right choice for your next project.
1. Consistent Material Flow and Pressure
One of the biggest advantages of using a pump system is its ability to provide a consistent and regulated material flow. Gravity-fed pot guns rely on gravity to feed the coating material into the spray gun, which can result in uneven flow, especially as the material level in the pot decreases.
Pump systems, on the other hand, maintain a constant pressure, ensuring that the material is delivered at a steady rate throughout the spraying process. This results in a more uniform spray pattern and a higher-quality finish, especially in applications requiring smooth, even coatings.
Key Benefit: Consistent flow ensures better spray coverage, less overspray, and a more professional finish.
2. Increased Capacity and Less Frequent Refilling
With gravity-fed pot guns, the capacity is limited to the size of the attached pot (typically around 600ml to 1000ml). This means that for larger jobs, you’ll need to frequently stop to refill the pot, slowing down productivity and potentially affecting the quality of the spray finish due to interruptions.
In contrast, pump systems can draw material from larger containers such as 5-gallon buckets or drums, allowing for much longer spray times without needing to stop and refill. This is particularly useful for high-volume applications like furniture manufacturing, cabinetry, or large-scale finishing projects.
Key Benefit: Increased material capacity reduces downtime and increases productivity.
3. Greater Versatility in Material Viscosity
Gravity-fed pot guns work best with coatings that are relatively thin and easy to flow. Thick or high-viscosity materials, such as certain types of lacquers, adhesives, or heavy-duty coatings, can be difficult to spray using a gravity-fed system.
Pump systems are designed to handle a wider range of material viscosities, as they force the material through the gun under pressure. This allows for greater flexibility in the types of coatings you can use, from thin stains to thick protective coatings.
Key Benefit: Pump systems can spray a broader range of materials, including high-viscosity coatings that may clog or struggle in gravity-fed systems.
4. Improved Operator Comfort and Efficiency
Gravity-fed pot guns can be cumbersome to handle, especially over long periods. The weight of the coating material sitting on top of the gun can make it more difficult to maneuver, leading to operator fatigue and reduced accuracy.
Pump systems are typically lighter because the spray gun itself doesn’t have to carry the weight of the coating. The material is pumped directly from a container to the gun, allowing the operator to focus more on precision and control without worrying about the added weight. This results in a more comfortable spraying experience and less fatigue during extended spraying sessions.
Key Benefit: Lighter, more ergonomic handling reduces operator fatigue and increases precision.
5. Reduced Overspray and Material Waste
One of the downsides of using a gravity-fed pot gun is the potential for overspray—when too much material is sprayed and misses the target surface, leading to wasted product and additional cleanup. Overspray is often caused by inconsistent material flow and uneven pressure.
With a pump system, the controlled flow and pressure minimize overspray by delivering the right amount of material consistently. This not only reduces waste but also helps in achieving a cleaner, more efficient application, saving both time and money on material costs.
Key Benefit: More efficient material usage reduces waste and lowers costs.
6. Ability to Work on Larger Projects
For large-scale projects, such as spraying walls, furniture, or extensive cabinetry work, using a gravity-fed pot gun can become inefficient due to the frequent need for refilling and the limited spray capacity.
A pump system allows you to work on larger surfaces continuously, without worrying about running out of material halfway through. This makes it the preferred choice for contractors, manufacturers, and professionals handling high-volume jobs where time and efficiency are critical.
Key Benefit: Pump systems are ideal for larger projects due to their ability to handle continuous spraying without interruptions.
Conclusion: Why Choose a Pump System?
While gravity-fed pot guns are practical for smaller, less demanding jobs, a pump system offers clear advantages in terms of consistency, capacity, versatility, and efficiency. Whether you’re working on large-scale projects or handling a wide variety of coatings, a pump system provides the durability and performance needed to achieve professional-grade results.
At the end of the day, investing in a pump system can save time, reduce material waste, and deliver a superior finish, making it a worthwhile upgrade for anyone serious about their spray finishing work.