How abrasive wide belts are made
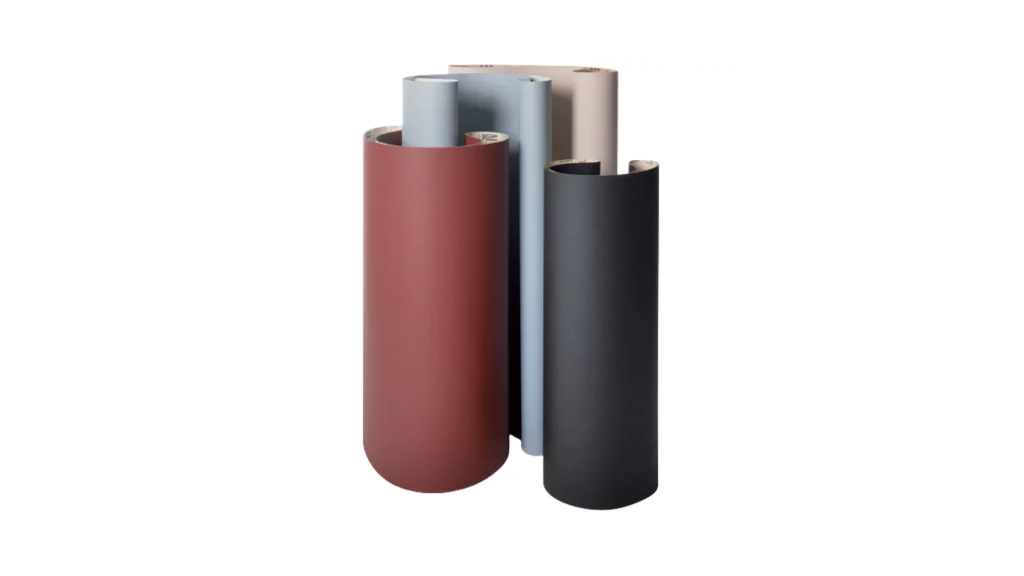
Abrasive belts are essential tools in various industries for sanding, grinding, and finishing applications, and their joints play a crucial role in their performance and durability. Several types of abrasive belt joints are commonly used, each offering specific advantages and considerations depending on the application and material being processed.
The overlap joint is a widely preferred choice, where one end of the abrasive belt overlaps the other and is bonded with adhesive. This configuration ensures a smooth and consistent sanding surface, particularly beneficial for woodworking where uniform finishes are critical. However, the overlapping area may create a slightly thicker section, which could affect precision tasks.
In contrast, butt joints, also known as tape joints, join the abrasive belt ends with adhesive tape, resulting in a flat and seamless connection. While this type maintains a uniform sanding surface without bulges, the adhesive tape can be susceptible to weakening under high stress or heat, necessitating regular inspection and maintenance.
Scarf joints involve cutting the belt ends at an angle and bonding them with adhesive to create a diagonal splice. This method provides a smoother transition and enhanced strength, making it suitable for applications requiring flexibility and durability. However, scarf joints are more complex to manufacture and align correctly compared to simpler joint types.
Finger joints feature interlocking fingers cut into the belt ends, bonded with adhesive to distribute stress evenly across the joint. This design offers strong mechanical bonding but is costly and less flexible compared to other joint types.
Lap joints are similar to overlap joints but with a shorter overlap length, reducing the risk of a thick seam. They provide good strength but may not withstand heavy usage as well as other joints.
Wavy joints incorporate a zigzag cut on the belt ends for increased bonding area, improving strength and flexibility. However, they are also complex to manufacture and align properly.
Lastly, skived joints involve thinning down the belt ends before overlapping and bonding, resulting in a smooth and thin joint area. This method minimizes raised sections but requires precise skiving and bonding techniques.
In conclusion, the choice of abrasive belt joint depends on factors such as required strength, flexibility, and the nature of the sanding or grinding task. Each joint type offers specific advantages and disadvantages, making it crucial to select the most suitable option for achieving optimal performance and longevity in industrial and hobbyist applications alike.